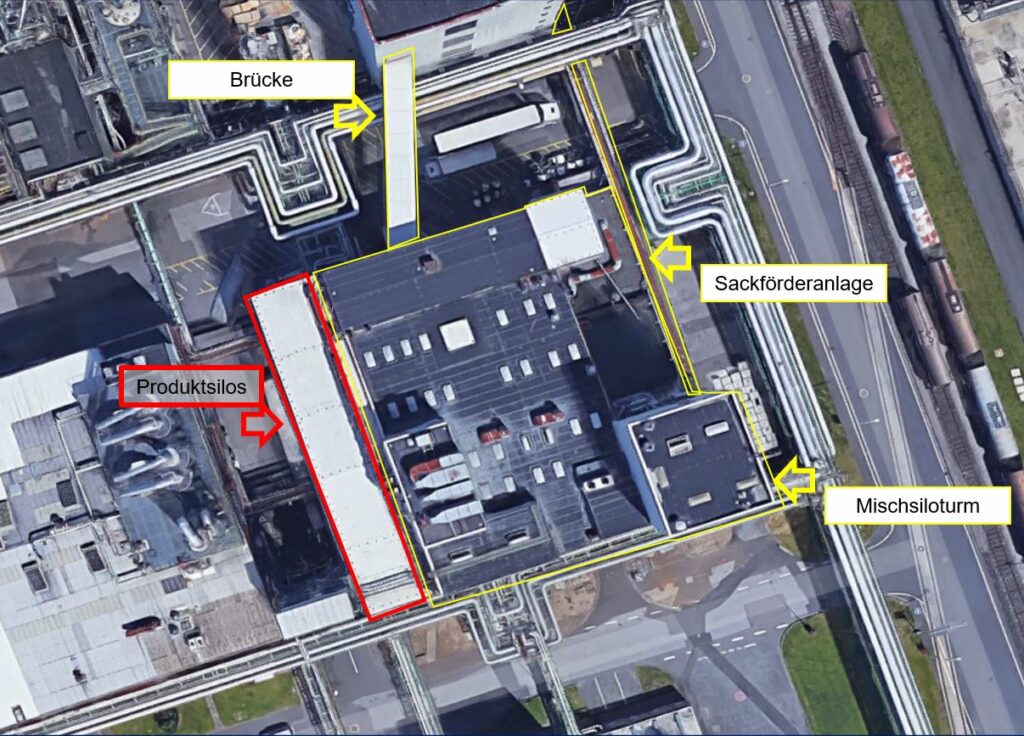
Selective partial dismantling in a chemical park during ongoing operations
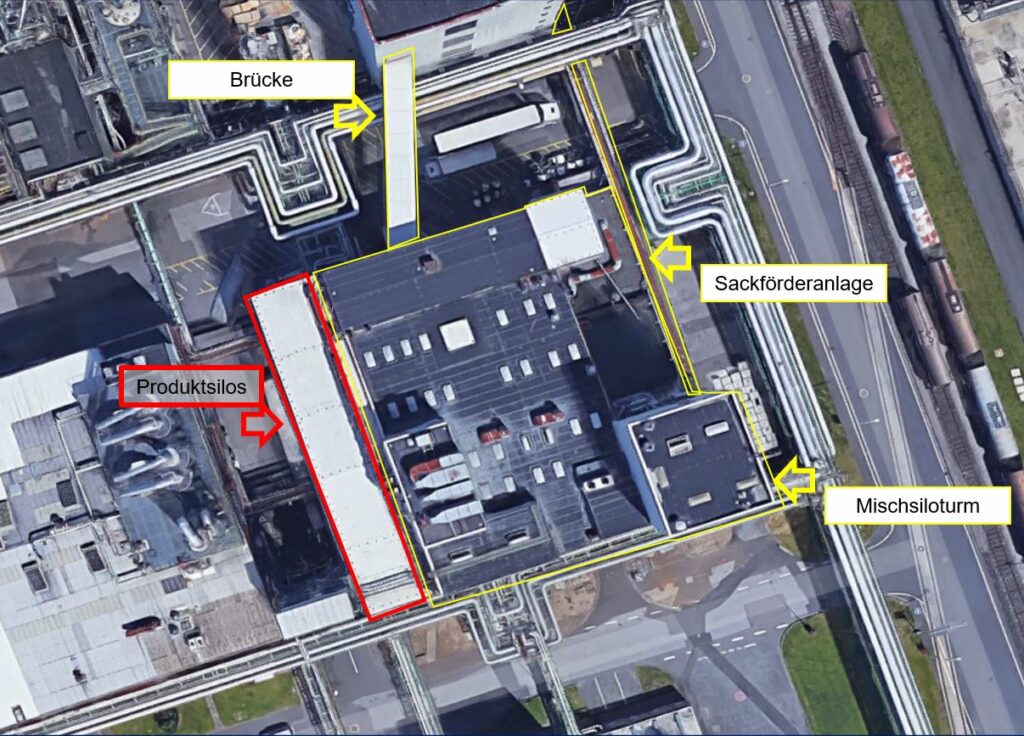
The dismantling of production facilities and buildings in a chemical park poses special challenges for planners and demolition contractors with regard to the appropriate demolition methodology and risk assessment.
On the one hand, the planning must enable effective and economic demolition using large equipment and, on the other hand, reduce the risks for the surrounding, neighbouring operating and production facilities to a minimum. This is done by means of a hazard assessment in which possible hazards/damage events are identified and their respective risks are assessed via the probability of occurrence and the estimated extent of damage. With this knowledge, risk-reducing measures are then determined.
There is neither a binding guideline nor a specific set of rules for the preparation of a risk assessment for a special demolion project in a chemical park during ongoing production. The procedure described here is based on tried and tested methods for identifying, classifying and assessing risks in industry and in the insurance sector.
The nomenclature and basic methodology are described in German and European standards for industrial plants, e.g. DIN EN ISO 121001 (formerly DIN EN 1050). The so-called Zurich Hazard Analysis (ZHA)2 should be mentioned as a further basis. The ZHA describes in an exemplary manner how risks can be assessed semi-quantitatively, i.e. on the basis of the extent of damage and the probability of occurrence. The ZHA also provides guidance on how a risk profile can be established and how risk reduction measures are taken into account. For example, the ZHA is recommended in a chemical industry guide3 as a best practice method for hazard assessment. The ZHA has proven its worth in determining the risk to people and the environment on the one hand, but also purely financial values such as business and product liability, property damage and business interruption on the other.
The risk assessment is carried out as an activity-specific risk assessment. The consideration extends to all phases and processes of the dismantling to be carried out.
The risk is determined quantitatively by estimating the probability (W) and the extent of damage (S) as well as the possibility of control (K). The extent of damage is divided into five categories.
Methodology
First step
The probability of occurrence (W) is qualitatively estimated in five categories. In the first step, the state without mitigation/protection measures is assumed as the initial state.
Likewise, the possibility of control (K) is qualitatively estimated in five categories. In the first step, the state without control/monitoring measures is assumed as the initial state.
Five risk classes are used to assess the risks.
Second step
In the second step, mitigation measures are defined for the expected hazards and a reassessment is made according to probability of occurrence and extent of damage. These mitigation measures include the establishment of appropriate project organisation and planning in terms of tasks and responsibilities to ensure safe operation of the works as well as
► the elimination or reduction of hazards,
► technical protective measures against hazards that cannot be eliminated,
► further organisational measures and
► personal protective measures.
The elimination or reduction of hazards as well as technical and organisational measures are given priority over personal protective measures.
Third step
In the third step, risk control measures (control and monitoring measures) are defined and a reassessment is carried out together with the possible mitigation measures. The goal is always to prevent the occurrence of the damaging event and/or to limit the risk to an acceptable level according to risk classes 1 and 2.
Practical example
The above methodology was carried out in practice by ERM GmbH in the context of a partial demolition of a three-storey, 19 m to 29 m high production building with an atached bridge.
The product silos, including the western loading zone, will remain in operation without interruption. The flanking pipe bridges, which are filled with gas, CO gas, ammonia liquid/gaseous, chlorine gas, hydrochloric acid, caustic soda, acrylonitrile, ethylbenzene, styrene, steam 30 bar, etc., belong to the CHEMPARK operator and supply the entire CHEMPARK. Therefore, shutdown, decommissioning and pressure reduction were out of the question. Swivelling over the pipe bridges with cranes is prohibited.
The basic demolition methodology and deconstruction sequence provided for decommissioning, gutting and decontamination first. This was followed by demolition of the building structure and disposal of the resulting demolition materials. For each activity of the respective deconstruction phases, a risk assessment and the determination of mitigation measures had been carried out with regard to the pipe bridge protection, the product silos to be preserved and the protection of the neighbouring buildings, as described above. This led, among other things, to
► a crane dismantling the 55 t connecting bridge by swinging it out, lowering it and dismantling it on the ground,
► the partial manual dismantling of the building façade from the working scaffold,
► the dismantling of the mixing pilot tower from the height +12.30 m after hot separation with a crane and further dismantling on the ground as well as
► the manual dismantling of the sand-lime brick lining Mischsiloturm.
A precise lifting and positioning plan prevented the cranes from tipping towards the pipe bridges. Damage to the pipe bridges by large, heavy falling objects was largely minimised by double-layer pipe bridge protection, partial manual dismantling and the use of impact mats. As an example, the risk analysis and assessment (step 1), risk reduction (step 2) and risk control (step 3) for the hazard “pipe bridge damage due to falling objects” looks as follows:
Step 1: Risk analysis and assessment
There is a high probability (W1=10) that without mitigation measures and control measures (K1=10), the pipe bridge and the pipes on it will be damaged during dismantling. This will result in a very large extent of damage (S=10).
The risk R1 = W1 * S * K1 = 10 * 10 * 10 = 1000 cannot be accepted (risk class 5, very high risk).
Risk mitigation measures shall be defined.
Step 2: Risk reduction
► Two-layer protective scaffolding over the pipe bridges
► Manual demolition from working scaffold and working platform (man basket crane)
► No overturning of the pipe bridges
► Lifting and positioning plan for cranes
► Use of impact mats
The mitigation measures make damage to the pipe bridges unlikely (W2=3, K2=10).
The reassessment leads to the risk R2 = W2 * S * K2 = 3 * 10 * 10 = 300 in risk class 3, medium risk.
Control measures shall be defined to further reduce the risk so that risk class 1, very low risk, is achieved.
Step 3: Risk governance
Permanent demolition monitoring with the involvement of the plant fire brigade
► Central shut-off valves and shut-off devices are staffed and prepared for shut-off
By monitoring and organising the shutdown, the hazard can be detected and mitigated at an early stage (W3= 3, K3=1).
The reassessment leads to the risk R3 = W3 * S * K3 = 3 * 10 * 1 = 30 in risk class 1, very low risk.
As a result, the described risk assessment for sensitive areas proved successful and the dismantling project could be realised without disruptions to production and accidents to all employees involved in the project and working at the Chempark.
Photos: ERM
Information
ERM GmbH
Thomas Wellmann
Technical Consulting Director
Siemensstraße 9
63263 Neu-Isenburg
Tel.: 0151 57 12 96 92
thomas.wellmann@erm.com
www.erm.com